水泥生产线中的窑尾锅炉(SP炉)在烟气热量的回收中,高灰分的烟气粉尘附着在受热面上造成锅炉的换热性能下降,出现粉尘塔桥、塌料,使系统的阻力增加,能耗增大。
SP炉通常采用传统的机械振打清灰。机械振打存在固有弊病,清灰存在死区、故障率高,影响了锅炉的效能。
一机械振打弊端
机械振打故障率高、维护量大:
1、锤头与振打杆接触面变形,电动机、减速机及相关的部件经常发生故障;
2、机械振打的备件损耗增加、停机检修时间增加、受热面的积灰增加;
3、锅炉的漏风点增加,热损耗增加。
二
SP炉清灰需求
1、清灰效果好,清灰无死角;
2、免维护、节省维修人员配置、节省备品备件费用;
3、无漏风点,无热损耗;
4、无接触式清灰,受热面无损伤;
5、运行可靠、省时、省力、省钱;
6、环保、节能降耗。
三
解决方案
1、声波清灰系统
它是以0.4~0.6Mpa 的压缩空气为动力源,使发声体内的钛合金膜片自激振荡,将压缩空气的势能转换成低频声能,使其发出低频、高能的声波,由空气介质传递到膨料点,作用到物料的分子结构内,使物料分子间结合力由紧密变为疏松,在重力或流体介质的作用下脱离附着体表面,达到了清灰的目的。
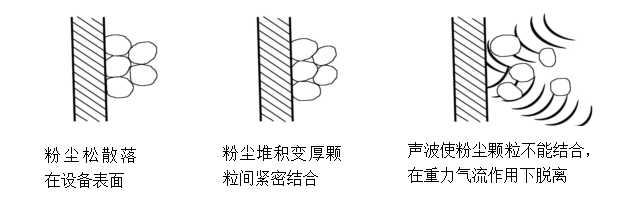
2、智能控制+物联网监控技术
物联网监控使采用无线远程传输模块将压力、温度、DI等检测仪表的输出信号进行采集,由系统进行智能化处理后提取特征数据,通过GPRS网络传回到云端。
监控系统可以实现实时远程监测数据:数值显示、连接状态显示、历史曲线查询、历史数据导出;多种报警条件:超限(或上限/下限)报警;利用云计算、物联网、大数据、人工智能等技术,实现了对声波清灰系统运行状态从感知到认知、从预测到决策的完整闭环监控。
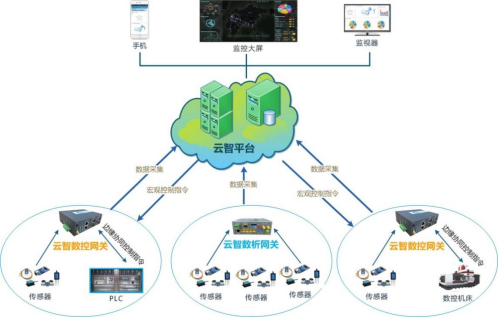
四
SP炉专用清灰产品
1、专用型声波清灰器
SQ-XWT型专用声波清灰器是辽宁中鑫自主研制、开发出来的专门用于水泥生产线中窑尾锅炉(SP炉)的清灰产品,它是基于传统膜片吹灰器技术,声功率级已达到 160dB+ 以上。
2、技术参数
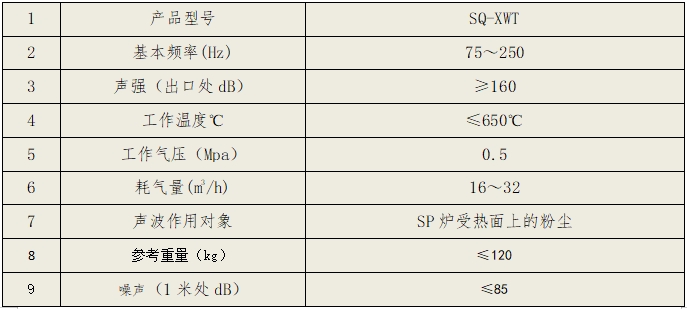
表1 声波清灰系统技术参数

表2 物联网智能控制系统技术参数
3、SP炉上的矩阵布置
声波清灰器在SP炉上的布置决定了受热面的清灰效果,辽宁中鑫根据SP炉的结构特点,锅炉内流体的速度、粉尘浓度、粉尘的粒径,粉尘在受热面上积灰的物理形状。经过专业技术人员长时间的分析、论证、实验,根据锅炉的规模,设计出了声波清灰器在SP上多种矩阵式的分布模式。
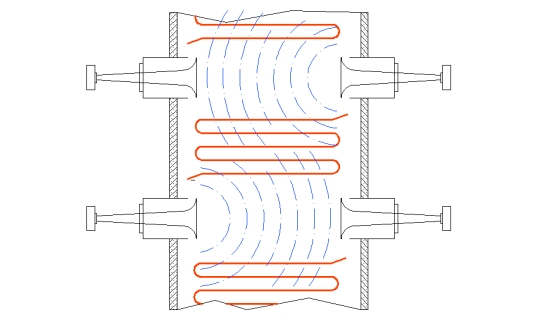
专用声波清灰器在炉墙上安装示意图
矩阵式的布局,使专用声波清灰器发出的声波经过导播筒放大后进入锅炉,声波顺着管束的方向传播,声能仅仅作用在流场内部受热面的积灰上,使声波在流场内部的传输通畅、声能损耗小,清灰效果达到最佳。
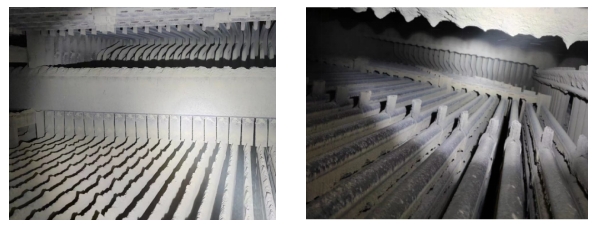
左图:声波清灰使用前
右图:声波清灰使用后
五
效果分析
辽宁中鑫SQ-XWT型SP炉专用声波清灰系统推向市场后,通过在华润集团属下多家水泥有限公司应用后,节能、环保效果显著,给企业带来了可观的直接经济效益回报,受到了企业的好评及推广。
1、替代料机械振打
2、节能降耗的效果分析
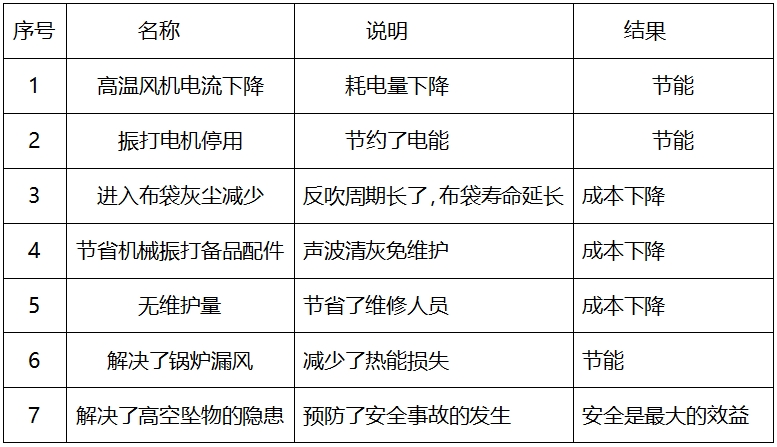
3、直接经济效益
按水泥生产线规模5000t/d,余热锅炉已经使用十年计算如下:
(1)8层机械振打,每层32个振打锤头,共计256个。每年更换200个×76元/个=15200元
(2)振打电动机+减速机,共计32套。每年更换10套×5500元/套=55000元
(3)机械振打人工维护费用,2人,每人日工资150元/日,运转率80%计算:150元/天×2人×365天×80%=87600元
每年直接经济效益:15000+55000+87000=157200元
六
安装服务
1、设计和制造周期
方案设计:1个工作日
实施设计:2个工作日
制造周期:2周
2、安装调试
公司指派专业工程师到现场指导安装、调试。
3、技术培训
对用户的相关技术人员和操作人员进行原理和操作培训,对声波清灰器易发故障的演示及处理方法培训。
4、质量保证和售后服务
一年内负责保修,免费维修或更换损坏的元器件。系统运行如出现故障,24小时内派专门技术人员到现场。
技术咨询
辽宁中鑫自动化仪表有限公司
谭总 18602603052
刘总 18010494526