2022年2月11日,国家发展和改革委员会发布了《高耗能行业重点领域节能降碳改造升级实施指南(2022年版)》的通知。作为高耗能行业之一的水泥行业,面临着深化节能降碳的挑战。
新规中,水泥行业节能降碳改造升级实施指南提到的推广节能技术应用就涉及:水泥厂高效节能风机/电机。
回转窑系统是水泥生产的心脏,而高温风机是回转窑系统的重要组成部分和最大的耗电设备。窑尾高温风机会将旋转窑内的余热废气引出,并通过预热器对进入窑尾前端的生料进行预热均化,降温后的预热废气又被高温风机抽出进行处理。通过调整窑尾高温风机转速,达到合理的回转窑内的气压和温度,进而保证煤粉充分燃烧和生料在回转窑内更好地煅烧。出于响应政策和降本增效的两个目的出发,企业需要调整高温风机以得到合理的风、煤、料匹配,进而达到最佳运行效果和降低生产能耗水平。
应用案例——高温风机运行现状
下表是我司重要客户某水泥厂在连续两年内高温风机运行参数及用电情况:
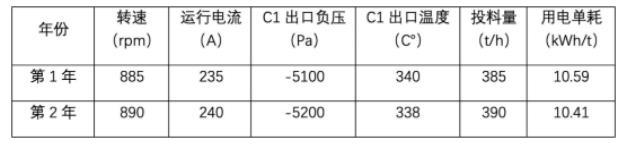
对于高温风机而言,仅仅从风机运行参数(转速、运行电流、C1出口负压、C1出口温度、投料量)和用电单耗,很难判断出用风的合理性,只是凭经验判断,C1出口温度有所偏高,系统用风应该存在富余,但缺乏理论依据。
操作人员使用testo 350 烟气分析仪,分别在分解炉出口、C1出口两个取样点进行抽取烟气,在高温风机正常运行885rpm下进行多次测量,数据如下表:
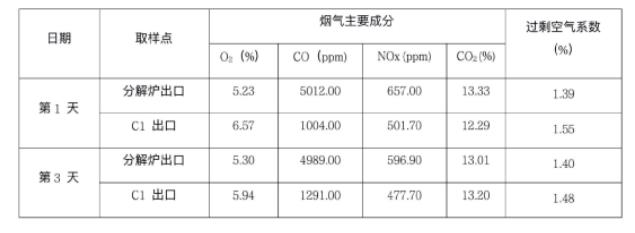
由数据看出,窑尾烟气成分中O2含量达到5.0%以上,过剩空气系数在1.45%左右,明显超出正常控制要求(正常情况下O2一般在0.7-3.5%,过剩空气系数一般在1.0-1.2%),这与之前根据C1出口温度判断的系统用风有所富余相吻合。另外,烟气测量结果中CO浓度偏高,NOx含量偏低,说明系统煅烧温度偏低,风、煤、料匹配不够合理。据此,企业生产运维人员认为非常有必要对高温风机转速进行降转调整,以确保系统用风的合理性。
高温风机运行调整
生产运维人员和操作人员协商采取循序渐进的方式降低转速,每次调整5rpm,且要保证系统稳定运行72小时以上,期间跟踪煅烧变化及熟料质量,每天测量窑尾烟气成分变化,烟气成分典型数据记录见下表:

通过烟气测量结果看,烟气中O2、CO浓度下降,CO2、NOx含量上升,空气过剩系数降至1.20%以内,另外C1出口温度下降约20℃,说明煤粉燃烧状况改善,系统风、煤、料匹配趋向合理。
针对NOx含量偏高现状,企业采取SNCR(选择性非催化还原)技术,确保NOx排放达到标准要求。
成效
调整前后高温风机运行参数及用电单耗对比见下表:
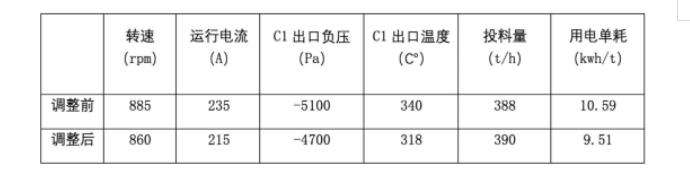
总体来说,经企业人员在近一个月内的调整,高温风机转速由885rpm逐渐降至860rpm,经企业生产运维工程师确认,烧成系统运行正常,台时产量、熟料质量未受到影响。
testo 350烟气分析仪蓝色新版本适用于烟气气体分析以及专业的工业排放测量。仪器坚固耐用,轻巧便携,适用于各种工况。中国版的公式计算得的燃烧参数,适用于中国的工况,并可以更简易的判断燃烧器的运行情况。正因为具有突出的耐高温、耐高粉尘、高精度传感器、便携性等诸多特点,才能胜任回转窑系统如此复杂的工况。
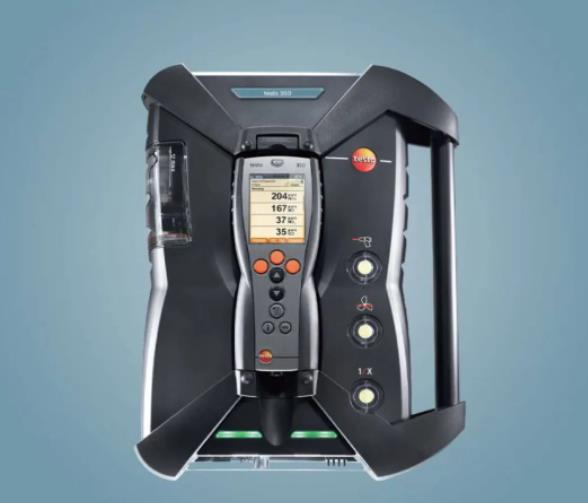
01高精度传感器
非分散红外原理CO2传感器;
电化学原理NOx,O2,CO,SO2传感器;
最多同时可装6个传感器。
02紧凑强劲的预处理/多级粉尘过滤
内置帕尔贴除水模块,简便地去除烟气中的水气,且在冷却过程中SO2/NO2损失非常低。也可叠加德图外置帕尔贴或外置加酸型预处理模块进行更高效地去除水气。主机机身上的精细过滤,采样探头软管和采样管前端都设置有过滤器,高效率消除烟气中的粉尘对测量仪器的影响。
03多种材质采样探头供选择
有多种不同可耐温度的探头类型供选择,有500℃、600℃、1000℃、1200℃、1800℃等。带有多级粉尘过滤模块,金属采样管长度最长可达3m,也有可调温式气路全程加热且能有效避免过程产生冷凝水的采样探头供选择,用于排放端高湿度烟气采样,所有探头可分段拆卸进行使用或维护。
更多业务欢迎咨询
400 882 0077
刘经理18010494526