近日,经地方推荐、专家评审,工信部原材料工业司发布2022年60个建材工业智能制造数字转型典型案例,涵盖信息技术供应商、系统解决方案、工业互联网场景、工业APP、智能工厂、数字矿山、单项应用等7个方向。
其中,邢台金隅冀东的设备远程在线监测系统、槐坎南方的水泥全流程智能化绿色工厂、桐庐红狮的水泥工业大脑、中建材的基于工业互联网的水泥智能生产管理APP等多个与水泥行业相关的智能化项目入选。
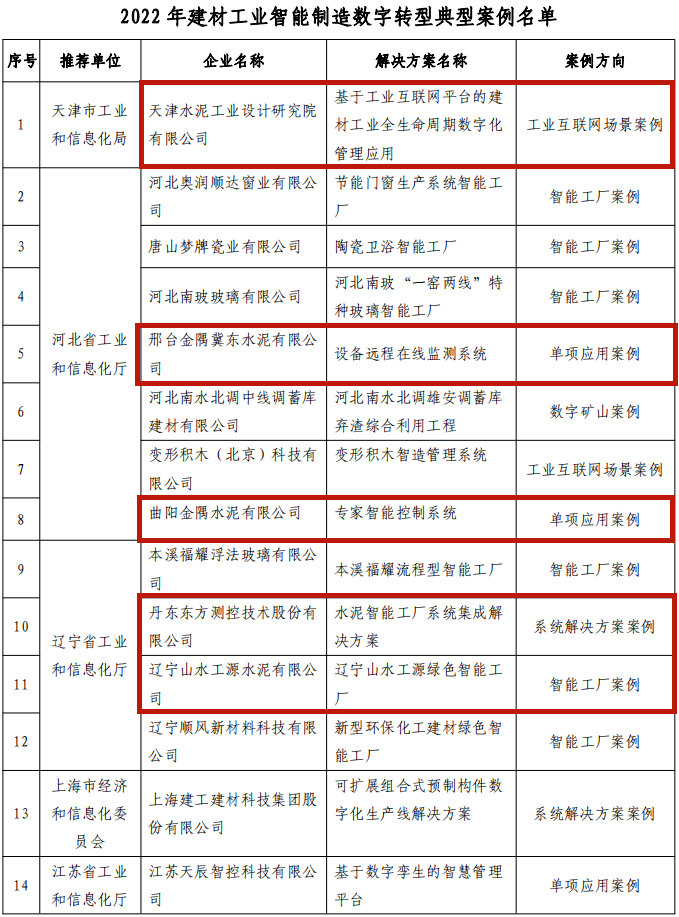

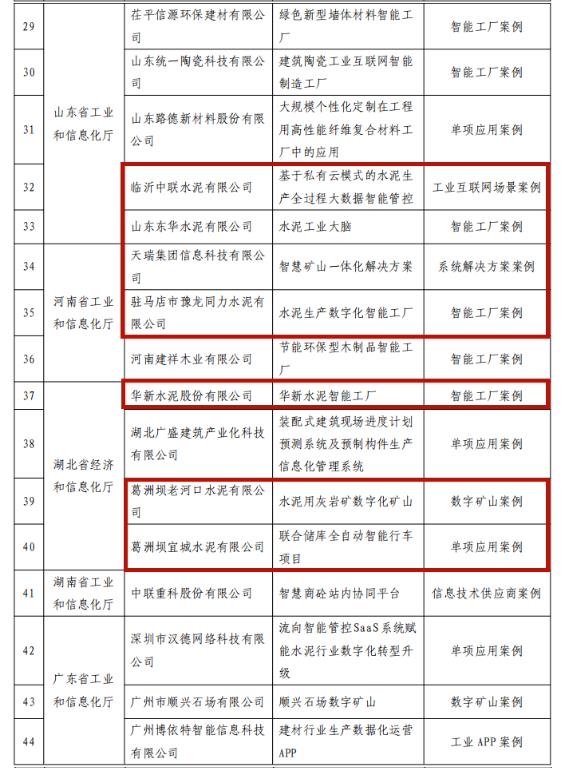

发布案例是为了落实《建材工业智能制造数字转型行动计划(2021-2023年)》(工信厅原[2020]39号),在行业内形成一批可复制、可推广的成果,宣传推广经验做法,推动建材工业与新一代信息技术在更广范围、更深程度、更高水平上实现融合发展。这些案例具有一定的代表性,为建材工业智能制造提供了有益探索。
此次发布的典型案例,不仅为水泥企业树立了标杆,更是再次从国家层面体现出水泥行业目前的发展趋势——数字化、智能化成为行业风向标。水泥企业必须深入挖掘生产运营数字化、智能化需求,持续探索水泥生产运营数字化转型升级路线。
《“十四五”数字经济发展规划》——我国数字经济领域首部国家级专项规划,聚焦建材、矿山、电力等重点行业“5G+工业互联网”应用,加快推进数字产业化和产业数字化,为尽快实现“数字中国、智慧社会”持续创新。
《建材工业智能制造数字转型行动计划(2021-2023年)》——到2023年修订30项以上建材行业智能制造相关标准,明确指出要促进水泥行业生产方式的自动化、智能化、无人化变革。
《“十四五”智能制造发展规划》——到2035年,规模以上制造业企业全面普及数字化网络化,重点行业骨干企业基本实现智能化。推动先进工艺、信息技术与制造装备深度融合,通过智能车间/工厂建设,带动通用、专用智能制造装备加速研制和迭代升级。研制一批国际先进的新型智能制造装备,研发新型干法水泥全流程智能化生产线成套装备。
全国多地也陆续出台智能化转型的指导细则:河南针对包括天瑞、中联、同力等52家水泥企业目前数字化等级制定了年度目标,要求到2022年底,全省水泥行业的数字化、网络化、智能化水平显著提升;重庆支持数字化车间、智能工厂、新模式应用、物联网等项目建设,对先进项目给予补贴奖励。
此次公布的智能化转型典型案例中,有的是智能工厂,有的是智慧矿山,还有智能装车、在线监测、设备巡检等多个智能化项目。对于整个水泥行业来说,都是非常具有参考价值的优秀案例,按照先进企业的经验进行改造,尽早完成数智转型,才能在未来的赛道中占得先机。
槐坎南方
槐坎南方是中国建材集团面向水泥行业碳达峰、碳减排目标重点打造的智能制造示范线,在水泥行业最先开展“数字化转型2.0”流程级两化融合贯标。秉承以智能装备、智能生产、智能运维、智能运营、智能决策为核心,以数据、算力、算法、场景和全链路的技术集群为技术驱动的理念进行生产管控智能化建设。
通过配置先进的在线分析检测设备,实现关键设备数控化率达到96%以上、生产数据自动采集率达到98%以上、烧成工序关键指标实时量化检测、过程质量数据高频检测、实现质量的预测和闭环控制;全面对接整合原有一卡通、办公系统等7个存量信息化系统,为智能控制系统、设备管理、能源管控、质量管控等21个新上子系统提供统一大数据仓库支撑,实现生产、能源、质量、设备、运维、备件、绩效、成本、采购等全生产运营流程的异构数据整合,生产数字化整合率达到98%。
临沂中联
近年来,临沂中联水泥有限公司不断加快新技术、新设备、新材料、新工艺的应用,对现有水泥生产线进行智能化技改提升,技改覆盖五大场景。
为推动数字转型,提高两化融合水平,公司开发智慧数据分析平台,该平台是基于私有云模式的水泥生产全过程大数据智能管控平台。为实现生产经营各系统数据互联互通,公司自建私有云,安装安超ArcherOS 2020服务器及分散控制系统,实现了机房的集约化管理,利用软件代替人工操作,稳定性得到提升。
同时,对高温风机、煤磨风机、罗茨风机等进行改造,改造后各项设备参数智能控制,节电效率提高25%以上。安装设备与人员安全监控管理系统,数据进入生产监控中心,提高了设备与人员安全管理水平。
安装生料在线分析系统、激光粒度分析仪及窑头热成像仪,大大提高了质量的稳定性。开发使用荧光仪MLD检测技术(熔片法),化学成分检验由机器代替人工,检验效率提高60%。安装设备状态在线监控系统、油品在线健康管理系统、电机健康管理系统,提高了设备预检预修能力,预防了大型设备损坏事故。
东华水泥
2018年7月,东华水泥同阿里云公司签订合作协议,联合成立山东东华智能制造研究院,全力研发全国首个水泥“工业大脑”,用数字赋能传统产业,让数据产生价值。
水泥工业大脑以大数据为核心,围绕水泥熟料生产的能耗优化、质量稳定,利用人工智能技术精准建模,寻求产量、质量、能耗之间的最佳控制参数,在不增加生产设备,不改变生产工艺的前提下,达到产量高、能耗低、质量稳定的目标。
山东东华水泥有限公司智能化工厂建设,以大数据驱动生产,把握“网络安全、数据安全”两大关键,建设智能安全生产系统、智能质控系统、智能物流系统、数字矿山系统、智能设备管理系统、智慧能源系统为六大子模块,通过连接DCS网络、工业传感器采集等方式获取生产过程中产生的大量数据,打破内外信息系统产生的物理数据孤岛,利用采集的历史数据进行优化模型建立、训练与验证,模型成功建立后,利用生产过程中的实时数据,对模型进行进一步的训练,直至模型拥有上线运行能力,通过DCS等工业自动化控制,实现模型的智能控制,水泥工业大脑与熟料生产深度融合,建设水泥生产的智能化工厂。
华新水泥
华新水泥万吨线智能工厂项目基于微波通讯、人工智能、云计算、大数据等前沿技术,研发应用智能行车系统、设备智能巡检系统、智能质量管控系统、水泥先进过程控制系统APC、数字一体化系统等,实现水泥生产全过程的数字化、可视化和智能化。通过营销数字化、智慧采购、智慧物流平台等系统,实现企业运营的数字化闭环管理。水泥综合能耗平均下降约4%,营销数字化平台销量占比高达95%以上,降低采购综合成本10%~20%,物流效率提升近50%。项目成果对我国水泥行业数字化建设具有重要示范作用。
吴忠赛马

数字化矿山、智能工厂、清洁能源利用等都是吴忠赛马在数字化、智能化方面全新的探索和实践。
吴忠赛马采用先进的机器人控制技术,实现了室内所有操作的无人化,24小时无人值守连续工作,并且每个操作环节都是高精度和高稳定性的,位置控制精度最高可达0.05毫米,同时实现了24小时连续取样及均化,保证了样品始终处于完全密封状态,不受外界环境的干扰,避免了样品的交叉污染,极大地提高了对工艺生产的指导作用。
数字化矿山将矿山资源、设备、人员、物资等全部数字化,利用卫星定位导航、物联网、数据库、无人驾驶、人工智能图像识别等先进的科学技术,实现矿山生产管理过程的科学化、智能化,以达到合理利用矿山资源、安全生产、低成本生产和高效管理的目的。
窑磨专家系统的使用,优化稳定了中控操作,节省了燃料和电力成本,提高了熟料质量的稳定性,显著提升熟料游离钙的合格率,减小水泥性能的标准偏差(凝结时间、强度等)。180台高清摄像机,全覆盖矿山、生产、销售、安防以及道路所有环节,通过数据传输,实现运行的动态监控、集中监控、异地监控,从而减小了操作人员劳动强度,降低了人员配置。