石灰石是水泥企业必不可少的第一原材料,它的品质关系着水泥熟料煅烧质量,最终影响到产品各项性能。近年来,南阳中联一直面临着自有矿山石灰石品位较低,结晶硅含量高,生料易烧性较差的难题,但南阳中联的质量管理人员笃定恒心,迎难而上,不断摸索和实践,通过加强原材料的质量管理、对生产过程严密监控、持续优化窑系统煅烧等措施,逐步扭转了这一现状,实现了利用低品位石灰石制备优质熟料的目标。
加强源头管理,保障原料质量均匀稳定
正本清源,方能引来源头活水。为保障进厂原材料质量,南阳中联把质量控制工序前移,从源头控制品质,严格落实《原材料质量验收标准》,加强进厂预检工作,一旦发现原材料外观异常、水分超标等状况,坚决予以拒收,杜绝了劣质原料进厂现象。
石灰石作为主要原料,更是当作质量管控的重中之重。南阳中联矿山结构复杂,夹层多、结晶硅含量高,质量主管王李均深入矿山现场,在每个开采点抽取样品化验分析成份变化,根据分析结果要求开采区域,并利用自动在线分析仪器,及时调整矿区开采区域,合理搭配高品位和低品位石灰石,使其满足配料要求。
通过长期的实践摸索,南阳中联逐步掌握了一套行之有效的经验方法,建立起矿山质检员和质量管理人员共同管理、在线分析仪实时检测、石灰石分品质使用、原料充分均化等四道质量防线,将质量管理和工艺管理有机结合,极大地保障了原料质量的均匀稳定,为保障熟料煅烧质量奠定了坚实基础。
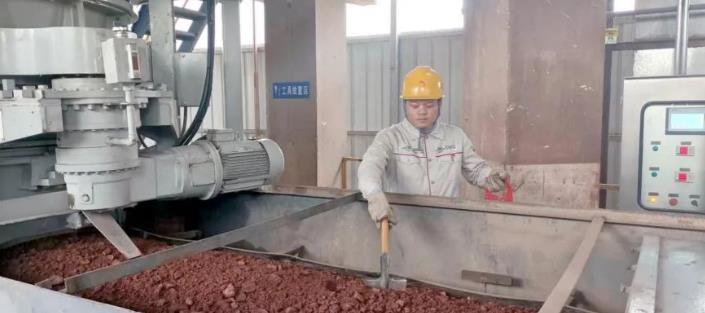
优化原料配比,保障生料制备科学精细
强化生料制备,科学优化配料,做精做细每一步。在生料制备过程中,南阳中联质量管理人员根据预均化堆场石灰石品位和窑的烧成状况,充分利用生料在线分析仪的质量控制优势,及时调整控制指标,科学优化配料方案。
同时,严格执行均化库使用管理制度,设置均化库使用曲线,确保均化设备正常运行且各区下料情况可追溯。只有在生料制备工序过程中每个质量节点做到有效监督,才能保证入窑物料均匀稳定,使其满足煅烧要求。
优化煅烧工艺,保障窑系统热工制度
精于工,匠于心,精细科学的煅烧工艺直接决定着出窑熟料的优质稳定。南阳中联制定了详实的工艺操作流程和管理制度,从预热器清理、窑头燃烧器温度控制、篦冷机用风等方面做出了具体的要求,并通过监督考核有效地保证落实。中控操作人员通过合理调整窑炉用风比例,使风煤料在预热器内充分反应,保证预热器系统温度持续稳定、物料充分分解、物理化学反应完全。窑头采用智能燃烧器系统,可根据窑前火焰温度及系统参数,实时判断窑况,并根据窑况对燃烧器进行实时调节,自动寻优。现场巡检人员每三天对预热器工艺点进行全面清理,确保系统安全顺畅。当物料到达篦冷机后,中控操作人员根据熟料温度情况,及时调整篦速和篦下用风,以确保熟料的快速冷却和热回收。
理论和实践操作不断证明,合适的生料成分,合格的细度控制,优质的煅烧环境,合理的矿物组成,这些对于熟料强度提高都是不可或缺的。凭借新设备新技术的引进,在中控员及现场人员通力协作配合下,南阳中联质量管理人员可以更加精准的掌握和优化生产工艺系统的工况,促使产能得以更好发挥,能耗得以有效控制,熟料生产基础进一步夯实,水泥熟料28d抗压强度得以实现60MPa以上。
强化过程管控,保障系统运行高效稳定
化验室是产品质量把关的核心部门,对生产质量的稳定和提高发挥着极其重要的中枢作用。为保障产品质量,化验室始终保持对异常数据敏感性,加强生产过程考核,保证各项指标完成合格率。定期进行生料易烧性试验,及时优化原料配料方案,每周进行熟料岩相分析试验,及时了解窑内的煅烧气氛、物料的煅烧情况和熟料的冷却情况,并进行及时改进,有效规避工艺过程中可能出现的问题。同时,化验室结合公司能源管理系统,利用微信、钉钉工作群,持续做好生产系统运行质量的比对分析工作,不断校正优化生产指标,保证质量控制的稳定性,这不仅实现了质量管理工作的可视化和即时化,也有效降低了三高三低或严重超差现象发生的频次。
凭借永不服输的信念,踏石留印的毅力,通过各个生产部门的紧密配合,各项措施的有效实施,南阳中联利用低品位石灰石参与配料成功制造出高品质水泥熟料,此制备方法被国家知识产权局授予发明专利。这不仅是南阳中联在资源综合利用、质量控制等方面取得的成绩,也对水泥行业的发展发挥了积极作用。在行业不断发展壮大的过程中,南阳中联将继续探索总结,形成更多可推广可复制的成功经验,为实现企业高质量发展和推动行业改革创新作出更大贡献。
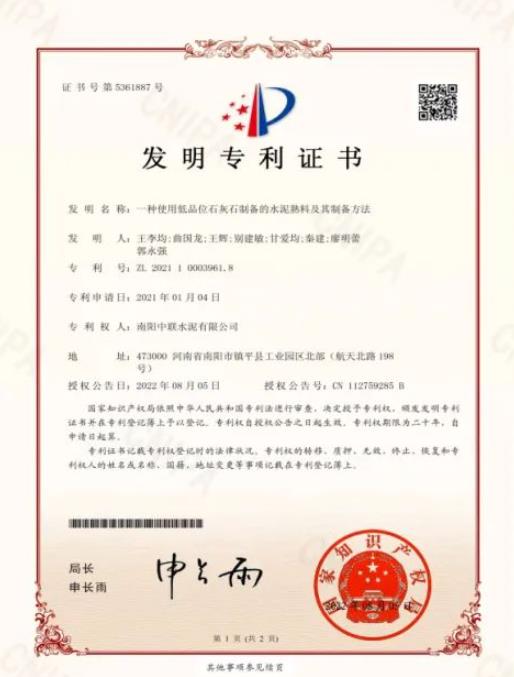
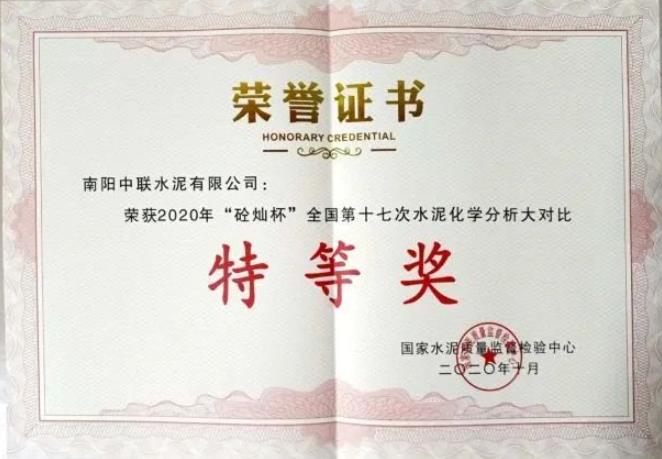
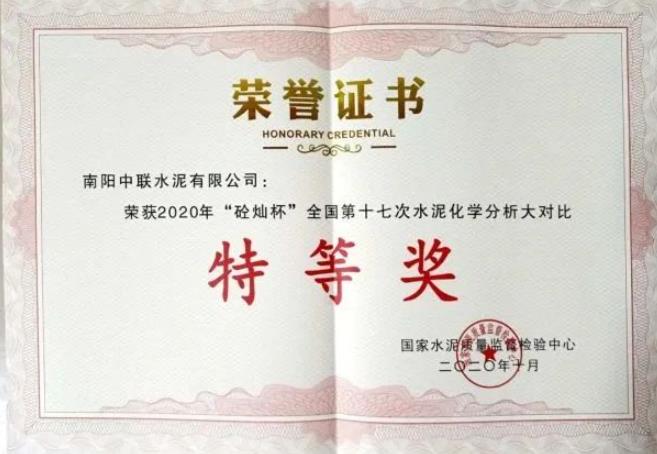
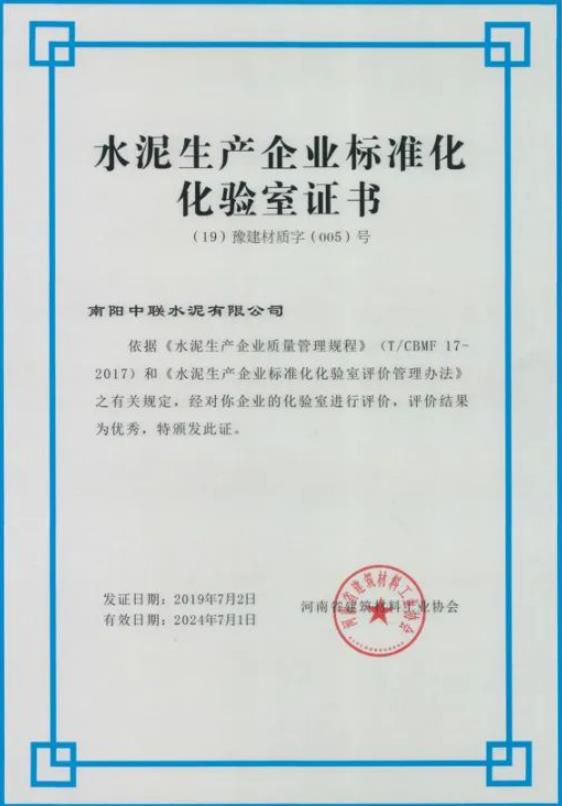
来源:中联同力